Now where do I start on this? It has definitely been a journey indeed! I love stickers and even before I started making my own I was an avid collector, sorting them into categories (usually animals being me) and using them in my journaling which is another passion of mine. As you can probably tell – putting my designs onto stickers was the most exciting product that I launched!
However, it’s been far from easy and I wanted to share some tips and tricks I’ve learned along the way so you can make your own sticker making dreams come true!
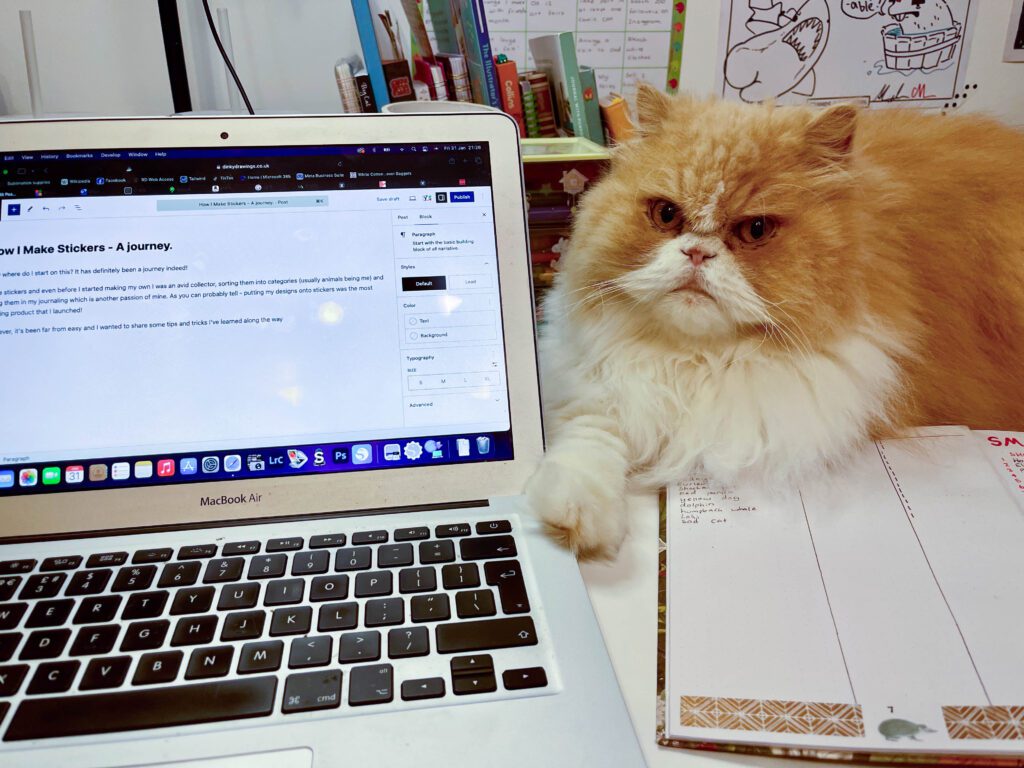
Ink
Personally I’ve tried laser printing stickers and using pigment ink. Both have worked really well. I find laser printing easier, as it’s much faster and you can print on a wider variety of papers. The toner is expensive but needs replacing less often. However, colour matching screen to paper is very difficult as I hear standard CMYK printers are and this could be very frustrating! Now we use an Epson R3000 series printer running 9 pigment inks. Thankfully as a keen photographer, this was something Michael already owned so it wasn’t an extra outlay to get started as these printers can cost a pretty penny. The ink costs were at first extremely expensive, but as we’ve gradually been replacing the epson inks with refillable cartridges the cost has gone down. These inks are beautifully coloured and we very rarely have to edit colours on the computer – I’d say 95% of the time, they come out as seen on screen. We’re currently using Marrutt refillable inks. They also have some excellent paper which are my favourite to do my a4 prints, but no sticker paper as of yet!
Paper
Evergreen Sticker Paper
The paper can make a big difference to the quality of the stickers, however I find that expensive papers are rarely needed. For a long time we’ve used Evergreen’s glossy white sticker paper which works on both inkjet and laser. They also have the advantage of being vegan and 100% recyclable! Unfortunately we couldn’t get it to work in our inkjet printer, perhaps because its a pigment one but worked perfectly with the laser once we figured out the settings. We found that turning the heat up to maximum on our Xerox 315 helped the stickers to bond correctly. I would then cut them out by hand. However, we started noticing that the stickers weren’t scratchproof and ink was coming off as they got scraped. We wanted them to be more resilient so people could enjoy them for longer.
Laminate
In comes many experiments with laminate! We started with hot laminate after watching a really helpful tiktoker- Tabs Art Shop on how she made her stickers. They coated beautifully and gave a lovely gloss to the stickers. However we had real problems with the stickers curling from the heat – I’m not sure if it was the 80gsm strength of our paper. I tried to flatten them under heavy books and by curling them to little avail and it was a lot of extra work! Eventually our trusted old laminator from the 2000’s failed and we had to get a new one. The new one did not work no matter what we did with it – everything we put through from paper to card melted and crinkled the plastic. We even tried to heat laminate in the heat press with some success, but the curling problem persisted.
One effective way of protecting the stickers was using an acrylic spray. Though it smells terrible when you use it, the smell fades quickly and it allows you to keep the flexibility of your stickers, unlike laminate.
Eventually we moved to cold laminate which Michael is an expert on. I’m unable to use it as I end up attaching it mostly to myself or the desk or most places that aren’t the sticker paper leading to stress. I’d also get a lot of bubbles trapped under the surface. However Michael thankfully has the knack and feeds it in quite serenely through the evil laminator which thankfully has a cold setting.
HTVRONT Vinyl Sticker Paper
Finally we arrived at vinyl sticker paper. I’d heard good things about HTVront and decided to give their paper a go. I’ve got to say I’m very impressed, the print is quality is beautiful and works on both inkjet and laser printers. The main advantage to this paper I’d say is that the designs are scratchproof and nearly nigh on waterproof. I experimented with this poor test sticker by scratching it with a coin and drowning it under my kitchen tap. This means I don’t need to add an extra protective layer which saves a lot of time and effort. Sometimes I may on my larger stickers if I want some extra rigidity but mostly I like my stickers to be flexible so people can use them on things like bottles. It does however have a problem with that it likes to curl as it goes through the printer, I’m not sure why. It is also letter size rather than A4 size, not a huge problem but worth noting as most things in the UK are set up for A4 size as standard.
The main thing I’d like to change is to make our stickers more environmentally friendly, but without compromising on durability. It’s a difficult situation and we’re constantly searching for ways to improve that.
Cutting Machine
Lastly we come to the cutting machine. Now you absolutely don’t need one of these, I was cutting my stickers out by hand for well over a year and apart from hand cramp it was fine. Eventually I was gifted one in 2024 and it has made sticker making so much quicker and easier, especially as we increased production. We work with a Silhouette Cameo 4. I’d write more about this but I absolutely suck at technology so Michael covers using that. So any questions regarding blade depth, speed etc, send us a message and he can tell you all about it. We’re still learning ourselves but we’ve pretty much got die cut stickers down and we want to start making some sticker sheets next.
Want to support my work and buy my stickers? You can find them here or browse my shop for lots of other cool things like t-shirts, keyring and cards.
Want to read more blogs and that kind of stuff? Sign up to the mailing list here!